Rebuilding and Restoration
Why choose us?
We have extensive experience in the rebuilding of vintage instruments especially Steinway, Mason Hamlin, Chickering, Knabe, Baldwin, as well as many fine European instruments. We customize each and every job to your own personal tastes and requirements, and we provide the necessary and comprehensive information for you to make informed decisions about your project.
Our goals are to create an instrument with the broadest dynamic and expressive tonal pallette, precision action performance, and a refined and detailed visual esthetic in every detail. In achieving these goals there are choices to be made: To put in a new soundboard or recondition the old one, which parts and hammers will achieve the tone and performance goals that you desire, whether to update or optimize the original engineering and design, where the weight and balance should be set, finish treatments, the list goes on. It can be daunting for the non technician to understand what all those options are, how the costs compare, what the likely tonal and performance outcomes will be. We will take the time to make sure you understand all the issues, options, costs and procedures that we propose to undertake to not only restore your vintage instrument to something as good or better than the original, but to customize the performance to your own personal needs and tastes.
Attitudes and approaches vary with respect to how to deal with 100-year-old designs and technologies, and customer goals do too. While there are many things to admire about the original designs of the great pianos of the early to mid 20th century, the evolution of the piano did not stop in the early 1900's nor were the originally intended executions necessarily achieved in the factory. Many of these same manufacturers continued to develop new design ideas and today there is a greater understanding of the acoustics of the piano, scale design, soundboard engineering, the elastic limits of materials used in soundboard construction that effect not only predictability of outcomes but longevity and stability as well. Touchweight standards and methods of discreet analysis have risen sharply in recent years as well. Options for optimizing designs are now routine with the benefit of engineered computer modeling that can help to predict better and more consistent outcomes. Depending on customer goals and attitudes we can duplicate original designs, optimize original designs or modify with enhanced performance features. Whatever your preference, we'll discuss the pluses and minuses and associated costs and help you make an informed decision.
We have extensive experience in the rebuilding of vintage instruments especially Steinway, Mason Hamlin, Chickering, Knabe, Baldwin, as well as many fine European instruments. We customize each and every job to your own personal tastes and requirements, and we provide the necessary and comprehensive information for you to make informed decisions about your project.
Our goals are to create an instrument with the broadest dynamic and expressive tonal pallette, precision action performance, and a refined and detailed visual esthetic in every detail. In achieving these goals there are choices to be made: To put in a new soundboard or recondition the old one, which parts and hammers will achieve the tone and performance goals that you desire, whether to update or optimize the original engineering and design, where the weight and balance should be set, finish treatments, the list goes on. It can be daunting for the non technician to understand what all those options are, how the costs compare, what the likely tonal and performance outcomes will be. We will take the time to make sure you understand all the issues, options, costs and procedures that we propose to undertake to not only restore your vintage instrument to something as good or better than the original, but to customize the performance to your own personal needs and tastes.
Attitudes and approaches vary with respect to how to deal with 100-year-old designs and technologies, and customer goals do too. While there are many things to admire about the original designs of the great pianos of the early to mid 20th century, the evolution of the piano did not stop in the early 1900's nor were the originally intended executions necessarily achieved in the factory. Many of these same manufacturers continued to develop new design ideas and today there is a greater understanding of the acoustics of the piano, scale design, soundboard engineering, the elastic limits of materials used in soundboard construction that effect not only predictability of outcomes but longevity and stability as well. Touchweight standards and methods of discreet analysis have risen sharply in recent years as well. Options for optimizing designs are now routine with the benefit of engineered computer modeling that can help to predict better and more consistent outcomes. Depending on customer goals and attitudes we can duplicate original designs, optimize original designs or modify with enhanced performance features. Whatever your preference, we'll discuss the pluses and minuses and associated costs and help you make an informed decision.
Rebuild or buy new?
If you've recently ventured into a new piano showroom you can easily feel and hear the great variation in touch and tone even between pianos of the same make and model. These differences are sometimes attributed to such things as "each piano's individual personality". While the inherent uniqueness of natural materials accounts for some of that variation, sometimes it simply reflects the inconsistency of predicted outcomes associated with certain methods on manufaturing. Through years of experience we have found that successful tonal output and precision action performance can be controlled consistently by careful analysis and engineering and controlled manufacturing. We can maintain those aspects of the original design that defined the tonal character of piano to begin with and then engineer each detail of the piano to create balance and uniformity through the scale enhancing the full dynamic range of the instrument. We think that a properly rebuilt piano can be, and often is, better than a new piano. That's because the attention to detail that we give is simply not found in most production manufacturing. As much as the original design allows, we tailor every aspect of the piano to your own personal taste, that includes both tone and touch and we can usually do it for less than the cost of a new one.
A typical restoration package includes:
Soundboard
When installing a new soundboard we analyze and engineer each one for optimum performance. Optimizations to the original execution are sometimes made when we find the factory did not achieve what may have been the original design goal. If the original soundboard still maintains enough structural integrity, we can, and do, recondition the panel to enhance stiffness in critical areas, resurface, repin and renotch the original bridge or install new bridge caps if necessary. All soundboards, old or new, are finished with traditional hand rubbed varnishes.
Scale
Each scale is analyzed and recalculated to insure accuracy of execution and smooth tension, inharmonicity and impedance curves for improved tonal balance.
Bridges
Bridges are either recapped or remade to accommodate the existing or optimized scales. Original bridges are routinely resurfaced, repinned and renotched to insure clean and solid terminations for tonal clarity.
Pinblock
For most restringing and all soundboard replacement jobs, we make, fit & install a new pinblock. On occasion the original pinblock can be reused but we do not recommend reuse for more than one restringing and then only if it is uncontaminated and structurally sound.
If you've recently ventured into a new piano showroom you can easily feel and hear the great variation in touch and tone even between pianos of the same make and model. These differences are sometimes attributed to such things as "each piano's individual personality". While the inherent uniqueness of natural materials accounts for some of that variation, sometimes it simply reflects the inconsistency of predicted outcomes associated with certain methods on manufaturing. Through years of experience we have found that successful tonal output and precision action performance can be controlled consistently by careful analysis and engineering and controlled manufacturing. We can maintain those aspects of the original design that defined the tonal character of piano to begin with and then engineer each detail of the piano to create balance and uniformity through the scale enhancing the full dynamic range of the instrument. We think that a properly rebuilt piano can be, and often is, better than a new piano. That's because the attention to detail that we give is simply not found in most production manufacturing. As much as the original design allows, we tailor every aspect of the piano to your own personal taste, that includes both tone and touch and we can usually do it for less than the cost of a new one.
A typical restoration package includes:
Soundboard
When installing a new soundboard we analyze and engineer each one for optimum performance. Optimizations to the original execution are sometimes made when we find the factory did not achieve what may have been the original design goal. If the original soundboard still maintains enough structural integrity, we can, and do, recondition the panel to enhance stiffness in critical areas, resurface, repin and renotch the original bridge or install new bridge caps if necessary. All soundboards, old or new, are finished with traditional hand rubbed varnishes.
Scale
Each scale is analyzed and recalculated to insure accuracy of execution and smooth tension, inharmonicity and impedance curves for improved tonal balance.
Bridges
Bridges are either recapped or remade to accommodate the existing or optimized scales. Original bridges are routinely resurfaced, repinned and renotched to insure clean and solid terminations for tonal clarity.
Pinblock
For most restringing and all soundboard replacement jobs, we make, fit & install a new pinblock. On occasion the original pinblock can be reused but we do not recommend reuse for more than one restringing and then only if it is uncontaminated and structurally sound.
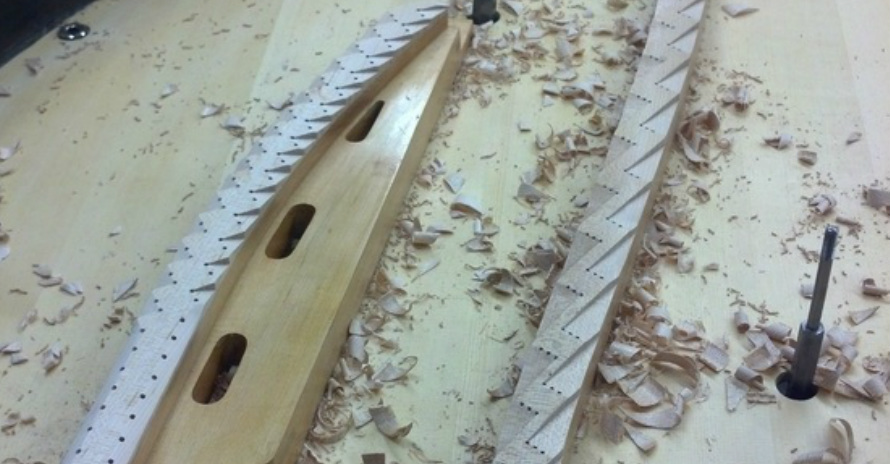
Plate
Plates are carefully cleaned, filled and sanded prior to refinishing. All agraffes are replaced, shaped and carefully polished. Counterbearing areas are analyzed for proper angles, reshaped, redesigned or replaced. Plates are refinished in gold and bronze lacquers with a protective clear coat. Lettering and plate decals are replaced as is consistent with the original design. Plate mounting systems and support dowels are typically upgraded with a modern plate suspension system that allows for fine adjustments of the plate height for more accurate downbearing settings.
Strings & Tuning Pins
Treble and bass strings are replaced with the highest quality wire available. Each set of bass strings is custom measured and ordered to insure absolute accuracy. We use Roslau Premium Wire in the plain wire section. Bass strings are custom made by the JD Grandt company to our specifications. We prefer traditional blued tuning pins but can choose nickel plating if the cosmetic requirements of the instrument or the customers demand it.
Plates are carefully cleaned, filled and sanded prior to refinishing. All agraffes are replaced, shaped and carefully polished. Counterbearing areas are analyzed for proper angles, reshaped, redesigned or replaced. Plates are refinished in gold and bronze lacquers with a protective clear coat. Lettering and plate decals are replaced as is consistent with the original design. Plate mounting systems and support dowels are typically upgraded with a modern plate suspension system that allows for fine adjustments of the plate height for more accurate downbearing settings.
Strings & Tuning Pins
Treble and bass strings are replaced with the highest quality wire available. Each set of bass strings is custom measured and ordered to insure absolute accuracy. We use Roslau Premium Wire in the plain wire section. Bass strings are custom made by the JD Grandt company to our specifications. We prefer traditional blued tuning pins but can choose nickel plating if the cosmetic requirements of the instrument or the customers demand it.
Action Parts and Hammers
We use the highest quality Renner action parts whenever possible. Hammers are chosen based on the tonal and performance requirements of the piano. Selecting hammers is a critical part of the rebuilding job and we take special care to sample a variety of hammers to insure that there is a good match between string tensions, soundboard response, and hammer characteristics. The hammers we most often use are: Ronsen Special Weickert Felt designed to our own custom specifications and various Renner hammers.
Each action is individually analyzed for leverage, inertia, geometry and alignment, weight and balance, regulation, friction and damper action interface. Action parts are selected in conjunction with the hammers to provide optimum balance, touchweight, and inertia. The dynamic balancing of the action is of paramount importance and issues of inertia and smooth touchweight characteristics are given strong priority in the selection of action parts to accompany hammer weight. While we do have a standard setting, all actions can be custom balanced to satisfy the needs of the individual player.
A complete action rebuilding includes changing not only the major action parts but all action supporting key frame felts, backchecks, leather, key bushings, etc. The action is fine regulated in the piano and installation includes a regulation follow up after the action has been adequately played in.
Voicing is a critical part of the set up process and considerations of customer tastes within the scope of the what the instrument can produce are given top priority. We are sensitive to varying tonal tastes. Final voicing is always done on site as the acoustics of the room or hall in which the piano is housed are a critical component in the voice of the piano.
We use the highest quality Renner action parts whenever possible. Hammers are chosen based on the tonal and performance requirements of the piano. Selecting hammers is a critical part of the rebuilding job and we take special care to sample a variety of hammers to insure that there is a good match between string tensions, soundboard response, and hammer characteristics. The hammers we most often use are: Ronsen Special Weickert Felt designed to our own custom specifications and various Renner hammers.
Each action is individually analyzed for leverage, inertia, geometry and alignment, weight and balance, regulation, friction and damper action interface. Action parts are selected in conjunction with the hammers to provide optimum balance, touchweight, and inertia. The dynamic balancing of the action is of paramount importance and issues of inertia and smooth touchweight characteristics are given strong priority in the selection of action parts to accompany hammer weight. While we do have a standard setting, all actions can be custom balanced to satisfy the needs of the individual player.
A complete action rebuilding includes changing not only the major action parts but all action supporting key frame felts, backchecks, leather, key bushings, etc. The action is fine regulated in the piano and installation includes a regulation follow up after the action has been adequately played in.
Voicing is a critical part of the set up process and considerations of customer tastes within the scope of the what the instrument can produce are given top priority. We are sensitive to varying tonal tastes. Final voicing is always done on site as the acoustics of the room or hall in which the piano is housed are a critical component in the voice of the piano.
Dampers & Damper Action
We make and install a new Renner damper tray assembly with underlevers routinely but can sometimes recondition the existing system if desired. The damper tray (see photo below) is typically modified with a fine adjustment capstan for each damper underlever for more accurate regulation.
Damper heads are cleaned, sanded and refinished or replaced if necessary. Guide rails are sized, refinished and rebushed. Damper felts are custom cut from the highest quality felt.
We make and install a new Renner damper tray assembly with underlevers routinely but can sometimes recondition the existing system if desired. The damper tray (see photo below) is typically modified with a fine adjustment capstan for each damper underlever for more accurate regulation.
Damper heads are cleaned, sanded and refinished or replaced if necessary. Guide rails are sized, refinished and rebushed. Damper felts are custom cut from the highest quality felt.
Lyre, Pedals & Trapwork
All felts and leather for the lyre, pedals and trapwork are replaced. Screws and pivot pins are polished or replaced. Older non-adjustable pedal rods are replaced with adjustable type. Pedal geometry is analyzed and corrected if needed and trapwork interface with the action is often modified for greater pedal efficiency, reduced friction and to control unwanted noise.
Casework & Finish
All finishes are done with the highest quality traditional, hand rubbed, lacquer. We work with you and the finisher to achieve the color and sheen that you desire. We manage all refinishing jobs from beginning to end. All hardware is polished, replated or replaced as needed.
All felts and leather for the lyre, pedals and trapwork are replaced. Screws and pivot pins are polished or replaced. Older non-adjustable pedal rods are replaced with adjustable type. Pedal geometry is analyzed and corrected if needed and trapwork interface with the action is often modified for greater pedal efficiency, reduced friction and to control unwanted noise.
Casework & Finish
All finishes are done with the highest quality traditional, hand rubbed, lacquer. We work with you and the finisher to achieve the color and sheen that you desire. We manage all refinishing jobs from beginning to end. All hardware is polished, replated or replaced as needed.